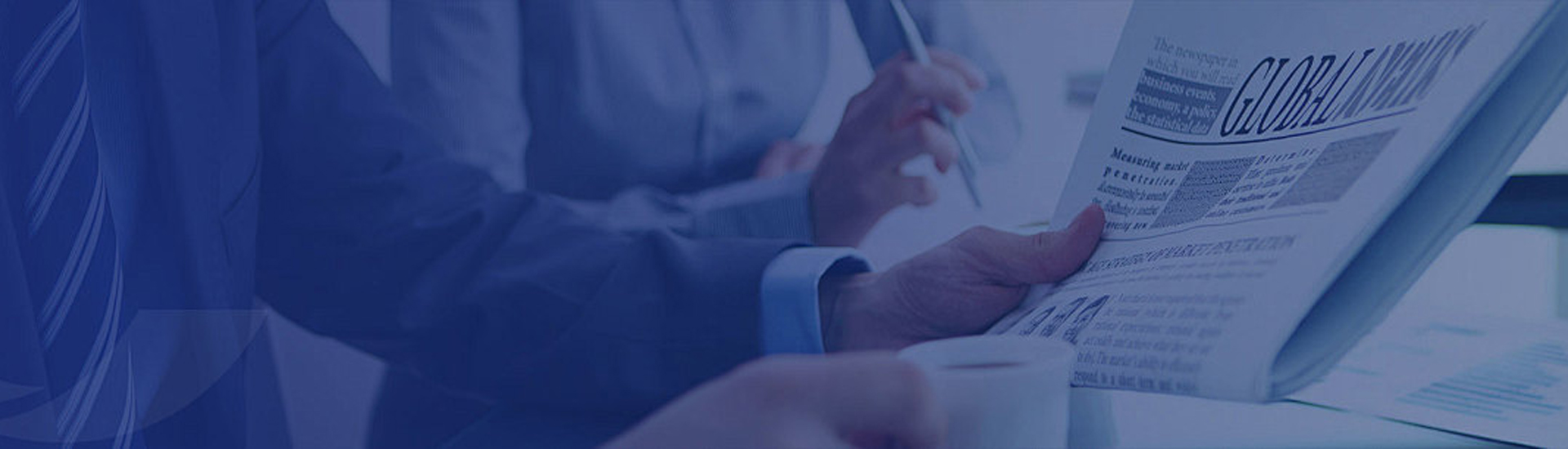
Cost control and benefit analysis of precision machining2024-10-31
Cost control and benefit analysis of precision machining
Precision machining, the process of removing material from a workpiece to create high-tolerance components, has become an essential part of industries such as aerospace, automotive, and healthcare. However, maintaining cost control while extracting maximum benefits poses a critical challenge for manufacturers. This article delves into how businesses can strategically manage costs in precision machining while unlocking its long-term benefits.
Precision machining, cost control, benefit analysis, manufacturing efficiency, CNC machining, ROI, lean production, operational efficiency
The Strategic Importance of Cost Control in Precision Machining
Precision machining is widely recognized as an essential process in the modern manufacturing landscape, producing highly accurate and complex components used in industries like aerospace, medical devices, and electronics. However, achieving the desired tolerances and surface finishes requires significant investments in advanced tools, skilled labor, and specialized technologies. Without effective cost control strategies, the benefits of precision machining may not translate into profitability.
1.1 High Precision, High Cost: The Challenges of Machining Excellence
Precision machining provides unparalleled accuracy, often working within tolerances as fine as a few microns. However, this accuracy comes at a price. Some of the biggest cost drivers in the process include:
Capital Equipment: CNC (Computer Numerical Control) machines, laser cutters, and EDM (Electrical Discharge Machining) systems require a high initial investment.
Material Waste: Precision machining often involves cutting away material from expensive raw stock, such as titanium or specialty alloys, leading to material waste if not optimized.
Tooling Costs: Advanced cutting tools and inserts are essential for achieving required tolerances, but they wear down quickly and must be replaced regularly.
Labor and Expertise: Skilled machinists and engineers are essential for programming, troubleshooting, and maintaining machines, but labor costs can be substantial.
These challenges make it clear that effective cost control mechanisms are required for sustainable growth in precision machining operations.
1.2 Cost Reduction Strategies in Precision Machining
There are several ways manufacturers can control costs without compromising quality or efficiency. Here are some practical strategies:
Optimizing Machine Utilization: Idle machines represent sunk costs. Manufacturers must implement scheduling strategies to minimize downtime and maximize equipment usage, such as predictive maintenance systems.
Reducing Material Waste with CAD/CAM Integration: Advanced CAD (Computer-Aided Design) and CAM (Computer-Aided Manufacturing) software allow for optimal nesting of parts and efficient material usage. Simulation tools can also predict machining outcomes to reduce scrap rates.
Investing in Multi-Axis Machining: Multi-axis CNC machines consolidate operations by allowing parts to be machined in one setup, reducing the need for multiple fixtures and reducing handling time.
Tool Lifecycle Management: Monitoring tool wear and using high-performance coatings can extend tool life, thereby reducing replacement costs. Some companies also adopt tool-sharing strategies with suppliers to further manage expenses.
Lean Manufacturing Principles: Implementing lean methodologies such as the 5S system can streamline workflows and reduce unnecessary movement of parts and materials within the production floor.
By applying these strategies, businesses can maintain tight cost control and ensure the profitability of their precision machining operations.
1.3 The Role of Automation and IoT in Cost Control
With the emergence of Industry 4.0, automation and the Internet of Things (IoT) are transforming how precision machining shops manage costs. Smart sensors embedded in CNC machines can provide real-time monitoring of parameters like temperature, vibration, and tool wear. This allows companies to conduct predictive maintenance and prevent unexpected downtime, which can be costly.
Furthermore, robots are increasingly used for loading and unloading materials, reducing labor costs and enhancing consistency. Automation also opens doors for lights-out manufacturing, where machines run unattended during non-working hours, further maximizing machine utilization.
1.4 Outsourcing vs. In-House Machining: Balancing Costs and Control
Companies often debate whether to perform precision machining in-house or outsource it to third-party suppliers. Outsourcing can reduce capital investment and labor costs, but it comes with risks related to lead times and quality control. On the other hand, in-house machining offers greater control but requires continuous investments in equipment and skilled workers. A hybrid approach—where businesses outsource non-core components while machining critical parts in-house—can often strike the right balance between cost control and operational flexibility.
In summary, precision machining offers incredible benefits but comes with significant cost challenges. By implementing strategic cost control practices—such as automation, material optimization, and lean production—companies can ensure that their precision machining operations remain competitive and profitable in a demanding market.
Analyzing the Long-Term Benefits of Precision Machining
While the costs associated with precision machining are significant, the long-term benefits outweigh the initial expenses when managed correctly. In this section, we’ll explore the financial, operational, and strategic advantages that precision machining can deliver over time.
2.1 Improved Product Quality and Brand Reputation
One of the primary benefits of precision machining is the ability to produce components with exceptional accuracy and consistency. This results in higher product quality, fewer defects, and greater customer satisfaction. In industries like aerospace or healthcare, where precision is non-negotiable, the ability to deliver high-quality products can elevate a brand’s reputation, leading to long-term business growth.
Precision machining also supports advanced quality control measures. With machine tools capable of holding micron-level tolerances, manufacturers can reduce rework and minimize returns, further enhancing profitability.
2.2 Increased Operational Efficiency and Faster Time-to-Market
Efficiency in production processes directly translates to better profit margins. Precision machining reduces the need for manual interventions, ensuring a more efficient and faster production flow. By leveraging technologies such as multi-axis CNC machines and CAD/CAM integration, businesses can shorten the production cycle, accelerating time-to-market for new products.
Faster delivery times can be a significant competitive advantage, especially in industries with short product lifecycles. Companies that invest in precision machining can meet tight deadlines without compromising quality, giving them an edge over competitors.
2.3 Lower Lifetime Costs Through Durable Components
Precision machining allows manufacturers to produce components with tight tolerances that fit seamlessly into complex assemblies. As a result, these components experience less wear and tear during operation, leading to longer product lifespans and reduced maintenance costs for end-users.
For instance, machined metal parts in automotive engines or medical devices last longer and perform more reliably compared to parts produced through less precise manufacturing methods. This improved durability translates to lower lifetime costs for customers, creating additional value that can enhance customer loyalty.
2.4 Scalability and Flexibility in Production
One of the unique advantages of precision machining is its scalability. Once a part is programmed into a CNC machine, production can be easily scaled up or down based on demand. This flexibility makes it possible for manufacturers to respond quickly to market fluctuations without incurring excessive costs.
Moreover, precision machining supports mass customization—allowing businesses to tailor products to individual customer needs while maintaining efficiency. This is particularly important in industries like healthcare, where customized medical implants or surgical tools are in high demand.
2.5 Environmental and Sustainability Benefits
Precision machining offers environmental benefits by minimizing material waste through optimized cutting processes. Advanced CNC machines, combined with CAD/CAM tools, help manufacturers cut only the necessary amount of material, reducing scrap and conserving raw resources.
Additionally, some precision machining processes use eco-friendly lubricants and coolants, minimizing the environmental impact. As more industries focus on sustainable practices, precision machining aligns with these goals by contributing to greener manufacturing.
2.6 Long-Term Financial Return on Investment (ROI)
While the initial investment in precision machining can be high, the long-term financial returns are substantial. Companies that invest in advanced machining technologies benefit from reduced labor costs, lower defect rates, faster production times, and improved product quality. These factors collectively result in a higher return on investment (ROI).
Precision machining also opens the door to new business opportunities, such as entering high-value industries like aerospace, medical devices, and robotics. By expanding their market reach and delivering superior products, companies can achieve sustained revenue growth and profitability.
In conclusion, precision machining, when executed with effective cost control strategies, provides a compelling pathway for manufacturers to balance expenses and maximize benefits. The combination of reduced operational costs, improved product quality, and scalability ensures that companies remain competitive in fast-evolving markets. While the upfront costs may seem daunting, the long-term financial and strategic advantages make precision machining a worthwhile investment for forward-thinking businesses.
By adopting lean practices, automation, and smart cost control strategies, manufacturers can turn the challenges of precision machining into opportunities for growth and success.