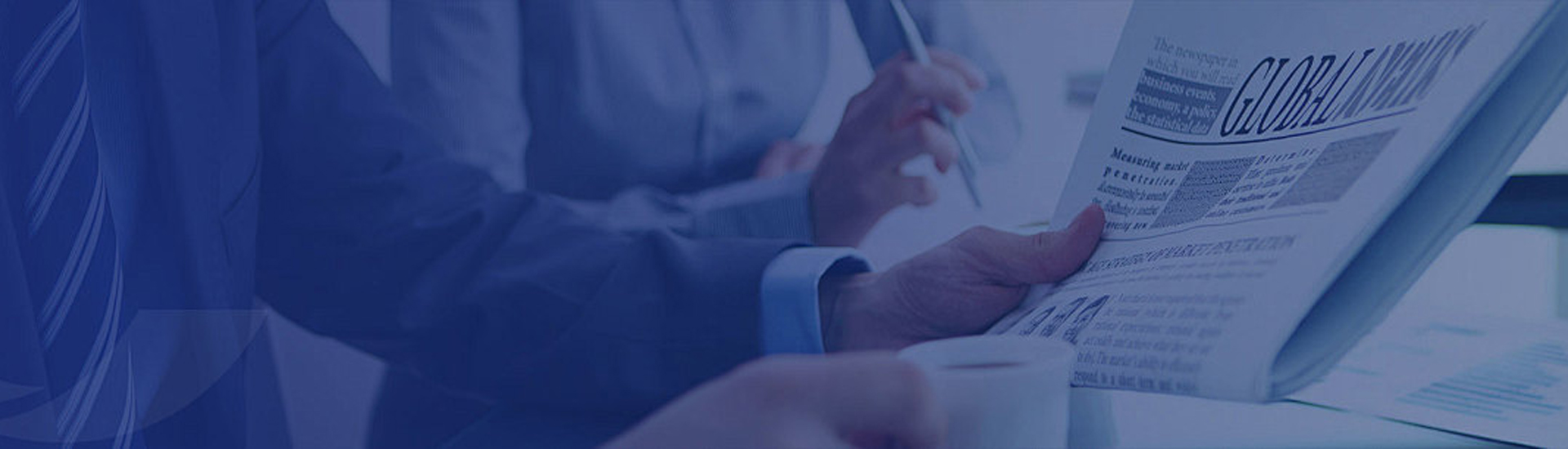
Challenges of Precision Machining in Aero Engine Manufacturing2024-10-30
Challenges of Precision Machining in Aero Engine Manufacturing
The Rising Demands of Precision in Aero Engine Manufacturing
In the aerospace industry, the evolution of aero engine design has pushed the boundaries of manufacturing technology, particularly in the area of precision machining. As demand for higher performance, fuel efficiency, and environmental compliance intensifies, so do the requirements for the manufacturing processes that make these complex machines a reality. Precision machining is one of the critical pillars in the production of aero engines, where even the smallest deviation can have massive consequences. Yet, despite its importance, this process is riddled with unique challenges.
Aero engines are marvels of engineering, composed of thousands of intricate components, each requiring exceptional accuracy. A single turbine blade, for example, may require tolerances within microns. The need for precision is non-negotiable; any deviation can lead to engine inefficiencies or, worse, catastrophic failure. Moreover, the operational environment of aero engines—high temperatures, pressures, and speeds—demands materials that can endure extreme conditions. These materials, such as titanium alloys, nickel-based superalloys, and ceramics, are notoriously difficult to machine. Herein lies the first significant challenge: how do you achieve such precision when the materials themselves resist machining?
Material Hardness and Heat-Resistant Alloys
One of the most significant issues in precision machining for aero engines is the hardness of the materials used. Aerospace components are primarily made from advanced alloys that are both lightweight and heat-resistant. These materials, such as Inconel or titanium, are designed to withstand extreme conditions but present unique challenges to machinists. For instance, nickel-based superalloys maintain their strength at high temperatures, but this same property makes them difficult to cut, leading to rapid tool wear and higher manufacturing costs.
Precision machining these materials requires advanced tooling and cooling systems. Conventional tools wear out quickly, often leading to poor surface finishes or dimensional inaccuracies. To mitigate this, manufacturers rely on carbide or diamond-coated tools, which can withstand the abrasive nature of these metals. However, even with advanced cutting tools, maintaining the tight tolerances required by aero engines is no small feat. High heat generation is another issue; without adequate cooling, the machining process can result in material deformation or thermal expansion, further complicating precision.
Tool Wear and Process Control
Tool wear is another crucial challenge in aero engine precision machining. Because of the toughness of materials used in aero engines, cutting tools degrade at a rapid rate. This wear impacts the quality of the machined surface and makes maintaining consistent tolerances difficult. Even the slightest variation in tool geometry can affect the precision of the final product. Regular tool changes are necessary, but this leads to downtime and increased costs, as machinists need to recalibrate the machines to ensure accuracy with each new tool.
Moreover, process control in precision machining is a monumental task. In industries where safety and reliability are paramount, such as aerospace, strict quality control protocols must be followed. Every component must undergo rigorous testing to ensure it meets exacting specifications. However, identifying defects and maintaining high-quality standards throughout the machining process is complex. Automated systems that monitor tool wear, temperature, and vibrations are used to ensure the process remains within acceptable limits, but even these systems are not foolproof.
Geometric Complexity and Surface Finish
The geometric complexity of aero engine components presents another layer of difficulty. Parts like turbine blades have intricate designs that require multi-axis machining to achieve. Machining these parts with precision often means accounting for compound curves, undercuts, and intricate internal channels, all while maintaining tight tolerances. Achieving the required surface finish is equally important; rough surfaces can lead to increased friction, reducing efficiency and potentially shortening the engine’s lifespan.
Achieving both geometric complexity and smooth surface finishes requires highly sophisticated machinery. CNC (Computer Numerical Control) machines equipped with multi-axis capabilities are standard in aerospace manufacturing, but the setup and programming of these machines require skilled technicians. Furthermore, maintaining consistency across large production runs without sacrificing quality or speed adds to the complexity.
Thermal Expansion and Distortion
Another challenge in precision machining for aero engines is thermal expansion and distortion. During the machining process, heat is generated from the friction between the cutting tool and the material. In the aerospace sector, precision is measured in microns, and even small changes in temperature can cause thermal expansion or contraction of the material being machined. This thermal distortion can lead to inaccuracies in dimensions, especially when working with large or long components.
Manufacturers combat this by employing sophisticated cooling techniques, such as flood cooling or cryogenic machining, where liquid nitrogen is used to maintain low temperatures during the machining process. However, managing thermal effects remains an ongoing battle. Advanced simulation tools help predict how materials will react to heat during machining, but real-world application still poses challenges. Factors such as tool speed, material removal rate, and environmental conditions all affect how much heat is generated and absorbed.
Vibration and Stability Issues
In precision machining, vibrations—or chatter—are another serious issue. These vibrations, caused by the interaction between the cutting tool and the material, can ruin surface finishes, compromise accuracy, and damage tools. The challenge is compounded by the rigidity required when machining hard materials like titanium or nickel alloys. The stiffer the material, the more prone it is to inducing vibrations, especially during high-speed machining.
Machinists use several strategies to reduce vibrations, such as optimizing cutting parameters, improving machine rigidity, and using dampening materials in the machine setup. Even slight adjustments in feed rates or spindle speeds can dramatically reduce chatter, but finding the optimal balance requires extensive testing and experience.
Tight Tolerances and Quality Control
Precision in aero engine manufacturing is not just about tight tolerances; it’s also about maintaining those tolerances over time and across multiple parts. Quality control in the aerospace industry is incredibly stringent, and every part must pass multiple layers of inspection. Non-destructive testing methods, such as X-ray or ultrasonic testing, are commonly used to check for internal defects that might not be visible to the naked eye. In addition, coordinate measuring machines (CMM) are used to ensure the final dimensions meet specifications. Even the smallest defect can result in the rejection of a part, leading to wasted material and time.
To ensure consistency, many manufacturers employ Statistical Process Control (SPC) techniques, where data from the machining process is continuously monitored to detect deviations before they become serious issues. However, this data-driven approach requires expensive equipment and highly skilled operators who can interpret the data effectively. The goal is to minimize human error and ensure that each part produced is identical to the one before it.
Environmental and Sustainability Considerations
In addition to technical challenges, aerospace manufacturers must also contend with increasing environmental pressures. Precision machining, particularly for complex materials, consumes significant amounts of energy and produces considerable waste. Recycling or reusing materials in the aerospace industry is difficult due to the high quality and safety standards required. However, the industry is moving towards more sustainable practices, such as using advanced cutting fluids that are less harmful to the environment and developing more energy-efficient machining processes.
Sustainability is becoming a major focus, with aerospace companies investing in green technologies to reduce their carbon footprint. Additive manufacturing, for instance, is being explored as a way to minimize material waste by building components layer by layer rather than cutting them from solid blocks. This shift not only saves material but also reduces the amount of energy required for machining.
In conclusion, the challenges of precision machining in aero engine manufacturing are multifaceted and complex. From handling tough materials and maintaining tool integrity to managing vibrations, thermal expansion, and environmental impact, the industry continues to push the boundaries of what is possible. However, with advancements in technology and innovative solutions, the future of precision machining in aerospace looks promising.