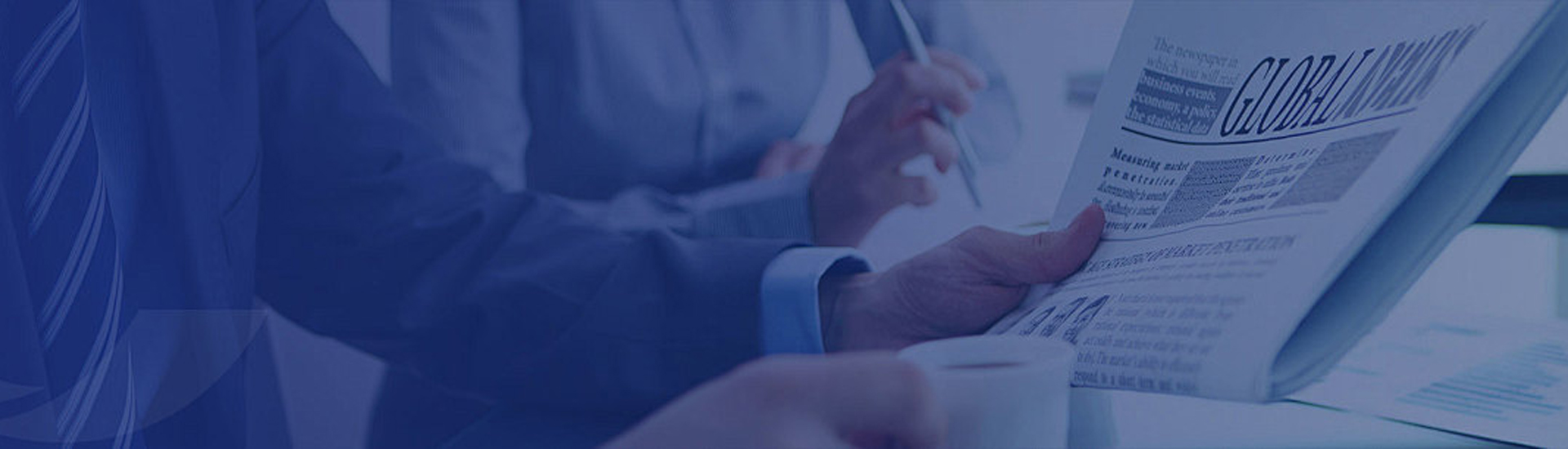
Automation and Intelligent Trend of Precision Machining2024-10-28
Automation is no longer just an emerging trend in precision machining—it has become a necessity. As global competition intensifies and consumer demand for higher-quality products increases, industries are turning to automation to enhance production capabilities, streamline processes, and reduce human errors. This shift towards automated solutions in precision machining is pushing the boundaries of what’s possible in manufacturing today.
At the core of this revolution lies the integration of advanced robotics and Computer Numerical Control (CNC) machines. CNC automation allows for high-precision operations to be executed with minimal human intervention, enabling manufacturers to produce complex parts with exacting tolerances. In industries such as aerospace, medical devices, automotive, and electronics, precision machining ensures the development of components that are not only accurate but also capable of performing critical functions reliably.
Incorporating robotics into the machining process is particularly impactful. Collaborative robots (cobots) work alongside human operators, optimizing workflow and reducing fatigue. Unlike traditional robots, cobots can adapt to various tasks, enhancing the flexibility of the production line. They are designed to take over repetitive, labor-intensive tasks such as material loading and unloading, tool changes, or inspection processes. As a result, the human workforce can focus on higher-level responsibilities, such as process monitoring, design optimization, and system management.
Moreover, automation helps overcome the increasing skills gap in manufacturing. As experienced machinists retire, fewer skilled workers are entering the field. Automated systems and AI-driven CNC platforms help bridge this gap by simplifying complex operations, allowing less-experienced workers to manage sophisticated machinery effectively. These automated systems also enable 24/7 production, significantly increasing throughput and reducing production lead times.
One of the key advantages of automation in precision machining is the ability to maintain consistent product quality. Automated systems, driven by pre-programmed specifications and real-time monitoring, ensure that every component is produced to exact standards, minimizing the risk of deviations or defects. This consistency is crucial in industries where even the smallest variance can result in product failure or safety hazards, such as in medical implants or aerospace components.
In addition to quality control, automation enhances overall efficiency and cost savings. Machine learning algorithms and real-time data analytics are now integrated into machining systems, optimizing cutting speeds, tool paths, and operational parameters on the fly. This leads to reduced cycle times and material waste, further driving down production costs. With predictive maintenance tools, manufacturers can also anticipate when a machine or tool might fail, minimizing unplanned downtime and ensuring continuous operation.
As industries increasingly embrace automated machining, they are reaping the benefits of improved scalability, higher productivity, and reduced operational costs. However, automation is just the beginning of the technological advancements reshaping the future of precision machining. The next phase involves integrating intelligent systems that leverage data, artificial intelligence, and machine learning to push the limits of what can be achieved.
The Rise of Intelligent Precision Machining: AI and Smart Systems
The fusion of artificial intelligence (AI) and intelligent systems with precision machining is setting the stage for the next wave of industrial innovation. Intelligent manufacturing systems represent the convergence of digital technology, advanced analytics, and machine learning, which is revolutionizing how we approach machining processes. This trend towards smart manufacturing is closely aligned with the principles of Industry 4.0, where data and connectivity take center stage.
In intelligent precision machining, AI plays a pivotal role in optimizing every aspect of production. AI-driven systems can analyze vast amounts of data collected from machine sensors and production lines to predict outcomes, adjust parameters, and learn from historical performance. By processing this data in real-time, AI enables machines to adapt autonomously to changes in material properties, tool wear, and environmental conditions, ensuring consistently high-quality results without manual intervention.
A notable example of AI integration in precision machining is the use of digital twins. A digital twin is a virtual replica of a physical machine or product, continuously updated with real-time data. Manufacturers can simulate machining operations in a digital environment, identifying potential issues and fine-tuning parameters before actual production begins. This minimizes costly errors, reduces the need for physical prototypes, and accelerates the development cycle.
In addition, AI-enhanced CNC systems enable predictive maintenance strategies. By monitoring machine health in real-time, AI can predict when a machine is likely to experience a fault or require servicing. This proactive approach reduces unexpected breakdowns, prolongs machine life, and minimizes costly repairs, contributing to more efficient and reliable production lines. Manufacturers can also use AI to schedule maintenance during non-peak hours, ensuring maximum machine availability during critical production windows.
Robotics, enhanced by machine learning, is also evolving in the intelligent machining landscape. Advanced robotic systems are capable of learning from previous tasks, improving their efficiency over time. They can autonomously perform complex machining operations, such as multi-axis cutting, grinding, and polishing, with minimal supervision. This leads to increased accuracy and consistency, especially in applications requiring intricate or non-standard geometries.
Beyond individual machines, intelligent precision machining extends to entire smart factories. Through IoT (Internet of Things) connectivity, machines, robots, and sensors are linked in a network that allows seamless data sharing and process synchronization. This interconnectivity enables manufacturers to track production in real-time, from raw material input to finished product output. It also facilitates remote monitoring and control, giving operators the ability to oversee operations from anywhere in the world.
The benefits of intelligent precision machining are far-reaching. For manufacturers, the combination of AI, robotics, and smart systems reduces operational inefficiencies and maximizes resource utilization. This leads to faster turnaround times, higher quality products, and improved competitiveness in global markets. Furthermore, the ability to customize machining operations dynamically opens new possibilities for personalized production, where products can be tailored to specific customer requirements at scale.
As we look to the future, the intelligent trend in precision machining is set to drive even more groundbreaking developments. Autonomous machining systems that require minimal human oversight, AI algorithms that continually improve machining performance, and real-time adaptive control systems are all on the horizon. In a world increasingly defined by speed, precision, and innovation, the role of intelligent machining in shaping the future of manufacturing cannot be overstated.
In conclusion, the automation and intelligent trend in precision machining are reshaping the manufacturing landscape. While automation has revolutionized efficiency and accuracy, the integration of AI and intelligent systems promises to take these advancements to new heights, enabling manufacturers to innovate faster, operate smarter, and compete on a global scale. As industries continue to evolve, those who embrace these technological trends will be best positioned to thrive in the competitive world of tomorrow.