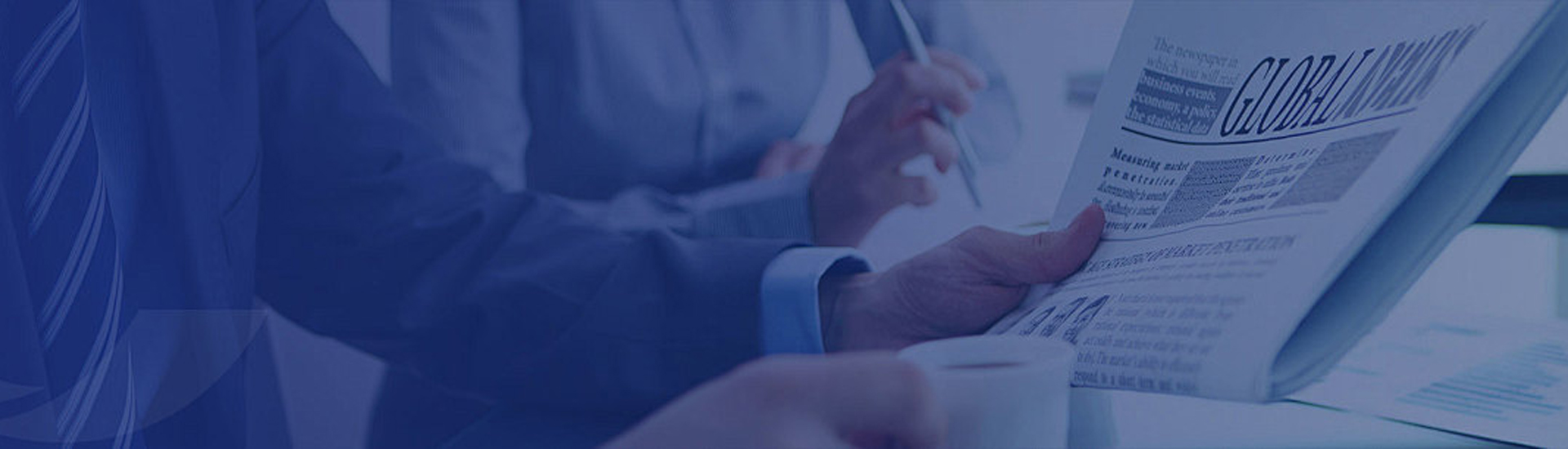
Application of precision machining in jewelry manufacturing2024-10-26
In the intricate world of jewelry design and manufacturing, precision has always been paramount. From the earliest days of hand-carving precious metals to today’s cutting-edge techniques, the drive for perfection continues to push artisans and manufacturers toward new technologies. One of the most significant breakthroughs in recent years is the application of precision machining in the production of jewelry. Precision machining, involving highly accurate cutting, shaping, and finishing of materials, is transforming the traditional craft of jewelry-making into a modern, high-tech industry while still preserving its core artistry.
The Role of Precision in Jewelry Manufacturing
Jewelry is, by its nature, both an artistic and a technical endeavor. Whether it's a pair of wedding bands, a diamond-studded necklace, or an intricate gemstone ring, each piece must meet demanding standards in both beauty and durability. The advent of precision machining technologies, such as CNC (Computer Numerical Control) machining and CAD/CAM (Computer-Aided Design/Manufacturing) systems, has provided jewelers with unprecedented levels of control and accuracy.
Gone are the days when an artisan had to rely entirely on their hands, vision, and basic tools to bring a design to life. Today, precision machining allows for minuscule tolerances, ensuring that every prong, clasp, and stone setting is as exact as possible. Not only does this boost the quality of the final product, but it also enables jewelers to push the boundaries of what is possible in design and structure. The results are jewelry pieces that are more intricate, precise, and customized to the client’s desires.
Benefits of Precision Machining in Jewelry Manufacturing
Unmatched Accuracy: Precision machining operates on incredibly tight tolerances, often within microns. In the context of jewelry, this level of accuracy means more reliable settings for gemstones, smoother finishes, and intricate detailing that would be impossible to achieve by hand. For example, an engagement ring crafted with CNC technology ensures the diamond is perfectly seated in the prongs, offering both aesthetics and security.
Enhanced Design Flexibility: One of the most significant advantages of precision machining is the creative freedom it gives designers. Using CAD software, designers can draft complex, three-dimensional models with detailed textures, patterns, and structures. These digital models are then fed into CNC machines, which can carve out the exact shapes from metal or other materials. This process allows for the creation of ultra-fine, intricate designs that are often difficult or impossible to handcraft.
Cost Efficiency: While high-precision equipment can represent a considerable initial investment, it greatly reduces labor costs over time. Tasks that once required hours of manual labor can now be completed in a fraction of the time, thanks to CNC automation. Moreover, precision machining minimizes material waste, as the computer-guided tools cut only what is necessary, optimizing the use of expensive materials like gold, platinum, or diamonds.
Customization and Personalization: With precision machining, jewelers can easily create custom designs tailored to individual clients. Whether a customer wants a unique engraving on a pendant or a custom-shaped wedding band, CNC machines can easily accommodate these requests. Additionally, CAD software allows clients to preview their designs digitally, offering them a chance to make adjustments before the actual manufacturing process begins.
Consistency in Mass Production: Precision machining also shines when it comes to producing jewelry in larger quantities. In traditional handcrafting, maintaining consistency across hundreds or thousands of pieces can be a challenge. Variations in craftsmanship, even by the most skilled hands, are inevitable. However, CNC machines can replicate the same design with absolute precision every time, ensuring that each piece of jewelry is identical in quality and appearance.
Precision Machining Techniques Used in Jewelry Manufacturing
Several advanced machining techniques are now widely used in the jewelry industry, each contributing to a more refined and efficient manufacturing process.
CNC Milling and Engraving: CNC milling machines are commonly used to carve out detailed patterns and shapes from metal. Whether it's engraving a family crest on a ring or milling out a bezel setting for a gemstone, CNC machines can handle these tasks with remarkable precision. For intricate designs that require deep carving or fine textures, CNC engraving tools are essential, allowing jewelers to add personalized touches without sacrificing quality.
Laser Cutting and Engraving: Laser technology is another key player in the precision machining revolution. Lasers are ideal for cutting metals like gold, silver, and platinum, as they offer precision without damaging the surrounding material. Laser engraving is also used to create detailed markings or patterns, offering a way to add highly intricate designs onto surfaces. The use of lasers allows jewelers to create precise cuts and engravings with minimal waste and time.
Water Jet Cutting: For more complex or delicate materials, water jet cutting offers a non-invasive way to shape and cut materials like precious metals and even stones. The ultra-high-pressure water jet ensures clean cuts without creating excessive heat that could damage sensitive materials, such as gemstones.
3D Printing and Casting: The integration of 3D printing in the jewelry industry has opened up a new realm of possibilities. Designers can create wax models using 3D printers, which are then used in the casting process to produce metal jewelry. This method allows for highly detailed prototypes to be made quickly, facilitating design adjustments before final production.
Precision machining, with its wide array of tools and techniques, enables manufacturers to create jewelry pieces that are both aesthetically pleasing and structurally sound. As these technologies continue to evolve, we can expect further enhancements in the speed, accuracy, and creativity of jewelry production.
While precision machining brings unparalleled technical advantages to jewelry manufacturing, its impact extends far beyond just production. The integration of these advanced technologies has redefined what is possible in terms of artistry, sustainability, and market competitiveness.
A New Era of Creativity in Jewelry Design
Precision machining has not only enhanced the technical aspects of jewelry manufacturing but also sparked a creative renaissance. Designers are no longer limited by the physical constraints of traditional tools. Complex geometries, intricate filigree, and even moving parts are now more accessible than ever.
Complex Geometries: The precision of CNC machining allows for the creation of designs with complex shapes that would be incredibly difficult to handcraft. From spirals and fractals to organic forms inspired by nature, precision machining gives designers the freedom to explore innovative shapes and structures. This newfound flexibility has led to the rise of more avant-garde, boundary-pushing designs in the jewelry world.
Micro-Engraving: With the ability to engrave at incredibly small scales, precision machining has opened up new possibilities in personalizing jewelry. Jewelers can now offer microscopic engravings, such as secret messages or initials, that are nearly invisible to the naked eye but can be appreciated up close. This technique adds an extra layer of meaning and intimacy to pieces like wedding bands, lockets, and signet rings.
Moving Parts and Kinetic Jewelry: Precision machining also allows for the creation of kinetic jewelry—pieces with moving parts, such as spinning rings, opening lockets, or adjustable bracelets. These designs not only add a playful and interactive element to jewelry but also demonstrate a new level of engineering skill in the craft.
Sustainability Through Precision
Sustainability has become a major concern across industries, and the jewelry sector is no exception. Precious metals and gemstones are finite resources, and traditional methods of jewelry-making can be wasteful. Precision machining addresses these issues by promoting material efficiency and reducing waste.
Optimized Material Usage: CNC machines are programmed to cut with extreme precision, meaning that only the necessary amount of material is removed. This contrasts with traditional methods, where excess metal is often shaved off or lost during production. With the cost of gold, platinum, and other materials at a premium, this reduction in waste translates into significant savings for both manufacturers and customers.
Recycling and Reusing: Modern precision machining also facilitates the use of recycled materials. Metals can be melted down and reused with minimal loss of quality, while CNC machines can work with these materials just as efficiently as new ones. This circular approach to materials ensures that less new metal needs to be mined, reducing the environmental impact of the industry.
Energy Efficiency: Many precision machining tools, particularly CNC machines, have become more energy-efficient over time. This not only reduces the carbon footprint of jewelry manufacturing but also lowers operational costs, making it a win-win for both the environment and the business.
Competing in the Modern Market
For jewelry manufacturers, precision machining is more than just a technical improvement—it’s a competitive advantage. The ability to produce high-quality, custom jewelry at scale, while maintaining consistency, has revolutionized the business model of jewelry production.
Faster Turnaround Times: Precision machining drastically reduces the time it takes to go from design to finished product. Once the CAD model is approved, CNC machines can work continuously to manufacture pieces quickly and efficiently. This faster production time allows jewelers to meet tight deadlines, such as for weddings, anniversaries, or special events, without compromising on quality.
Customization as a Market Differentiator: Today’s consumers are looking for personalized experiences in every aspect of their lives, and jewelry is no different. Precision machining allows manufacturers to offer bespoke, custom-made pieces at prices comparable to standard collections. This ability to meet the demand for one-of-a-kind jewelry sets a business apart from competitors that rely solely on mass-produced designs.
Consistent Quality Across Products: Whether producing a single custom ring or a batch of a thousand necklaces, precision machining ensures that each piece meets the same high standards of quality. This consistency builds trust with customers, as they know they are receiving a product that has been crafted with care and precision.
The Future of Jewelry Manufacturing
As precision machining technologies continue to evolve, we can expect to see even more exciting developments in the world of jewelry manufacturing. The integration of artificial intelligence (AI) and machine learning into CNC systems could further enhance the design process, offering predictive modeling and real-time feedback on structural integrity. Additionally, as sustainability becomes an increasingly important consideration, we may see more advancements in eco-friendly materials and energy-efficient production techniques.
Ultimately, the application of precision machining in jewelry manufacturing is more than just a technological upgrade—it’s a transformation of the entire industry. By combining traditional craftsmanship with modern precision, jewelers are crafting pieces that are not only more beautiful and durable but also more sustainable and accessible to a wider audience. This fusion of art and science ensures that jewelry will continue to be a timeless expression of beauty, love, and innovation for generations to come.