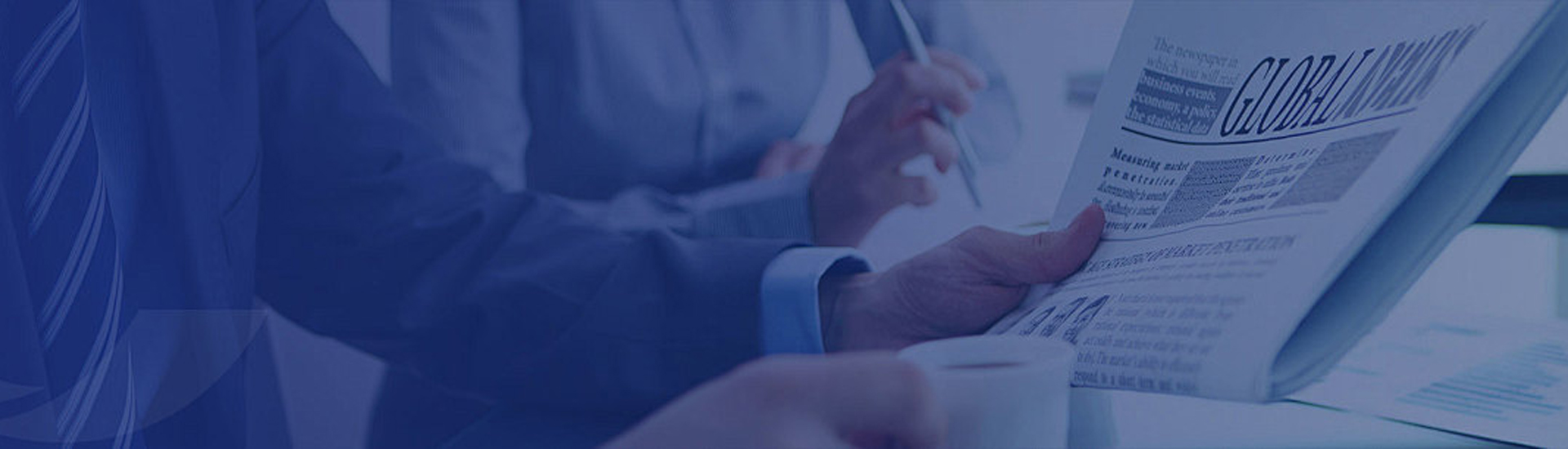
The key technology of high-precision machining2024-10-24
Explore the transformative world of high-precision machining, uncovering its key technologies, applications, and future prospects. Discover how precision is revolutionizing industries and enabling the creation of intricate designs that drive innovation.
High-precision machining, technology, applications, CNC machining, manufacturing, industry innovation, future trends, automation, materials, quality control.
High-precision machining represents a pivotal evolution in the manufacturing landscape, characterized by the ability to produce components with extremely tight tolerances and exceptional surface finishes. This technology is not merely an enhancement of traditional machining methods; it embodies a holistic integration of advanced tools, techniques, and methodologies that collectively elevate the standards of production across various sectors.
Understanding High-Precision Machining
At its core, high-precision machining is defined by the ability to achieve measurements within micrometers, enabling the creation of parts that fit seamlessly in complex assemblies. Industries such as aerospace, automotive, medical, and electronics heavily rely on this technology to meet stringent performance and reliability standards.
Key Technologies Driving High-Precision Machining
CNC Machining: Computer Numerical Control (CNC) machining stands as the backbone of high-precision manufacturing. By using computer-aided design (CAD) software, CNC machines execute complex cutting operations with minimal human intervention. This automation not only enhances precision but also significantly boosts production efficiency. The accuracy of CNC machines, often reaching tolerances of ±0.001 mm, makes them indispensable in high-stakes applications.
Electro-Discharge Machining (EDM): This non-traditional machining process utilizes electrical discharges to remove material from a workpiece. EDM is particularly effective for hard materials and intricate geometries that are difficult to machine with conventional tools. Its precision is unparalleled, making it ideal for applications requiring fine detail, such as in molds and dies for the automotive and aerospace industries.
Laser Machining: Employing high-powered lasers, this technology enables cutting, engraving, and marking with extreme accuracy. Laser machining is notable for its speed and versatility, capable of working with various materials including metals, plastics, and ceramics. The precision achieved through laser technology often allows for the creation of complex shapes that were previously unattainable.
5-Axis Machining: Traditional machining methods typically involve three axes (X, Y, Z) for movement. However, 5-axis machining adds two additional rotational axes, allowing for intricate and complex geometries to be produced in a single setup. This technology significantly reduces the need for multiple setups, minimizing errors and enhancing production efficiency.
Advanced Materials: The rise of high-precision machining has coincided with the development of advanced materials. Composites, titanium alloys, and other high-performance materials demand precision machining to achieve the desired properties and performance. The ability to machine these materials accurately is crucial for applications where weight, strength, and durability are paramount.
The Importance of Quality Control
As the stakes for precision increase, so does the necessity for rigorous quality control. High-precision machining requires a robust quality assurance framework that includes real-time monitoring and inspection techniques. Tools such as coordinate measuring machines (CMM) and laser scanning technology enable manufacturers to ensure that every component meets the exact specifications. This emphasis on quality not only reduces waste and rework but also instills confidence in the reliability of the final products.
Applications Across Industries
The applications of high-precision machining are vast and varied. In the aerospace sector, components such as turbine blades and landing gear must be produced with exacting standards to ensure safety and performance. Similarly, in the medical field, high-precision machining is essential for creating surgical instruments and implants that can withstand rigorous conditions.
The automotive industry also benefits immensely from high-precision machining, particularly in the production of engine components, transmission parts, and safety features. The integration of high-precision techniques allows manufacturers to produce lightweight and fuel-efficient vehicles that meet environmental regulations while maintaining performance.
The Future of High-Precision Machining
The landscape of high-precision machining is continually evolving, driven by advancements in technology and shifting market demands. As we look to the future, several key trends are emerging that will further shape this field.
1. The Rise of Automation and Smart Manufacturing
The integration of automation in high-precision machining is accelerating. With the advent of Industry 4.0, manufacturers are embracing smart technologies that facilitate real-time data analysis, predictive maintenance, and enhanced workflow efficiency. Automation not only minimizes human error but also allows for 24/7 production capabilities, driving down costs and increasing output.
Robots equipped with advanced sensors and machine learning algorithms are now capable of performing intricate tasks alongside traditional machines. These systems can adapt to changes in production conditions, ensuring consistent quality and precision.
2. Additive Manufacturing and Hybrid Technologies
While subtractive machining has long dominated the precision machining landscape, additive manufacturing is gaining traction as a complementary technology. The ability to print complex geometries using materials such as metals and plastics opens new avenues for design and production.
Hybrid machining processes that combine additive and subtractive techniques are emerging, allowing for the creation of parts with intricate internal structures while ensuring the necessary surface finishes. This synergy can lead to more efficient designs, reduced material waste, and improved performance characteristics.
3. Sustainable Manufacturing Practices
As environmental concerns continue to rise, the manufacturing industry is shifting towards more sustainable practices. High-precision machining is increasingly incorporating eco-friendly materials and processes. Techniques that minimize waste, reduce energy consumption, and lower emissions are becoming standard practice.
The focus on sustainability also drives the development of biocompatible materials for medical applications, ensuring that the components produced are safe for human use and environmentally friendly.
4. Enhanced Materials and Coatings
The ongoing research into new materials and coatings is poised to revolutionize high-precision machining. Advanced ceramics, composites, and coated tools enhance the performance and longevity of machined components. These innovations not only improve machining efficiency but also extend the life of tools, reducing downtime and costs.
Additionally, surface treatments that enhance wear resistance and reduce friction are becoming critical in high-precision applications. These advancements lead to improved performance and reliability, particularly in harsh operating environments.
5. Customization and Rapid Prototyping
As consumer demands shift towards personalization and customization, high-precision machining is adapting to provide rapid prototyping and small-batch production capabilities. This flexibility allows manufacturers to respond quickly to market trends and customer preferences, facilitating innovation and maintaining competitiveness.
The ability to produce customized components without sacrificing precision or quality opens new markets and applications, particularly in industries such as fashion, consumer electronics, and bespoke manufacturing.
Conclusion: The Impact of High-Precision Machining
High-precision machining is more than just a technical process; it is a vital component of modern manufacturing that drives innovation and progress. By leveraging cutting-edge technologies and embracing new methodologies, industries can push the boundaries of what is possible, creating products that are not only precise but also transformative.
As we continue to explore the frontiers of high-precision machining, the implications for industries, economies, and society at large are profound. With each advancement, we pave the way for a future where precision is not merely an attribute but a fundamental expectation in the manufacturing process. Embracing these technologies will enable us to meet the challenges of tomorrow, ensuring that we remain at the forefront of innovation and excellence.