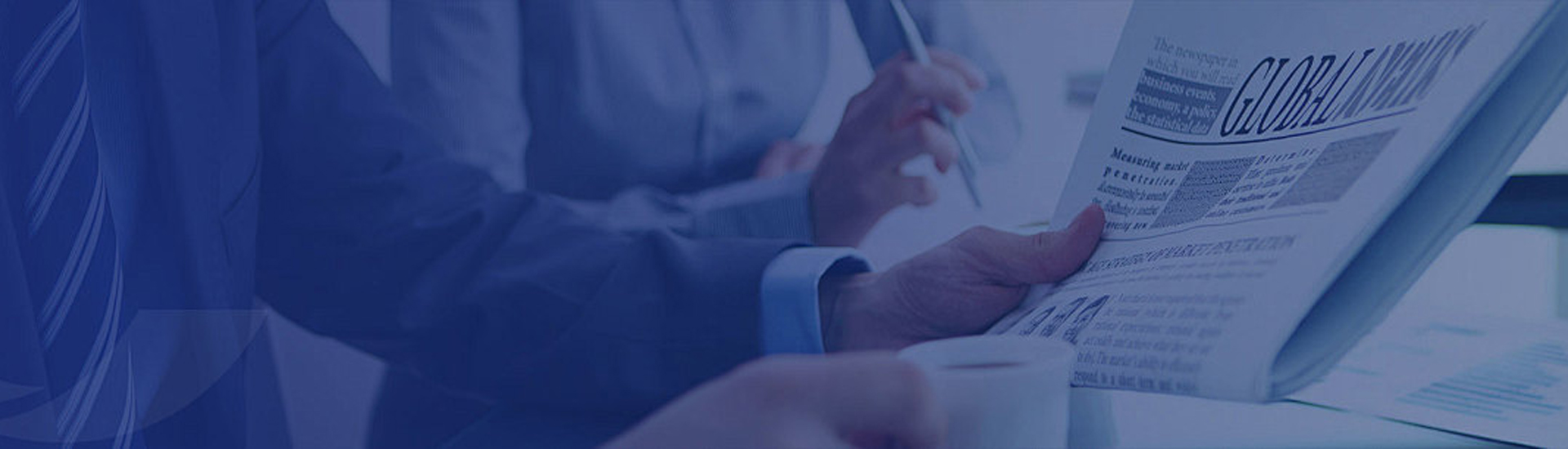
Innovation and Development of Precision Machining Technology2024-10-23
The ever-evolving field of precision machining technology is at the core of global industrial advancement. Whether in aerospace, medical devices, automotive manufacturing, or electronics, precision machining has become an indispensable element that empowers companies to produce parts and components with unmatched accuracy. In a world where tolerances are growing tighter, and quality demands are skyrocketing, the innovation and development in this technology are opening new doors to possibilities that were once deemed unattainable.
1. The Backbone of Modern Manufacturing
At its essence, precision machining involves using advanced techniques and machinery to produce components that require extremely tight tolerances, often measured in micrometers. These components are critical in industries where reliability, safety, and functionality are non-negotiable. The ability to machine with such high precision ensures that parts fit together perfectly, function efficiently, and maintain structural integrity, especially under challenging conditions.
Innovations in precision machining have played a vital role in improving the quality and capabilities of products in various fields. For example, in the aerospace sector, precision machining is essential for manufacturing critical components such as turbine blades, engine parts, and structural elements that must perform flawlessly under extreme temperatures and pressures. In the medical field, precision machining allows for the production of highly intricate surgical instruments, implants, and diagnostic equipment that demand unparalleled accuracy.
2. Digital Transformation: Smart Machining Systems
A significant driver of innovation in precision machining has been the advent of digital technologies, particularly Computer Numerical Control (CNC) machining and smart manufacturing systems. CNC technology has revolutionized the way precision machining is performed by allowing for the automation of complex machining processes. It eliminates human error while significantly increasing efficiency, flexibility, and scalability.
In modern CNC systems, machine learning (ML) and artificial intelligence (AI) are being integrated, allowing machines to self-optimize during operations. These intelligent systems can predict tool wear, reduce downtime, and adapt to changes in real-time, leading to reduced production costs and enhanced product quality. Additionally, the rise of Internet of Things (IoT) and Industry 4.0 is enabling precision machining equipment to communicate with each other through connected networks, further enhancing operational efficiency.
3. Advancements in Materials and Tooling
Alongside digital innovations, the development of new materials and cutting-edge tools has further expanded the capabilities of precision machining. Traditionally, metals like steel, aluminum, and titanium have been the primary materials used in precision machining. However, the innovation of advanced materials such as composites, ceramics, and superalloys has pushed the boundaries of what is achievable. These materials offer improved strength, heat resistance, and longevity, making them ideal for high-performance applications.
Furthermore, the tools used in precision machining have also seen significant enhancements. Diamond-tipped tools and ceramic-based cutting tools are now used to achieve unparalleled precision and durability. These tools are designed to withstand higher speeds, intense temperatures, and long machining durations, all while maintaining cutting accuracy.
As industries continue to demand even higher levels of precision and complexity in the components they require, the development of precision machining technology must evolve in tandem. Innovations in areas such as additive manufacturing, automation, and sustainability are now converging to push the boundaries of precision machining, promising a future where the impossible becomes a reality.
1. Additive Manufacturing and Hybrid Machining
One of the most exciting developments in the precision machining world is the fusion of additive manufacturing (3D printing) with traditional subtractive machining techniques. Known as hybrid machining, this process combines the strengths of both methods to create highly complex parts with superior precision and material efficiency. In a hybrid system, a component can be 3D printed layer by layer using metal powders or polymers, and then precision-machined to meet exact specifications.
This approach opens up new design possibilities and enables the creation of intricate geometries that would be difficult or impossible to achieve using conventional machining alone. For instance, hybrid machining is being used to produce lightweight yet highly durable components for the aerospace and automotive sectors, where weight reduction is crucial for fuel efficiency and performance. By blending additive and subtractive technologies, manufacturers can reduce material waste, optimize energy usage, and produce components with faster turnaround times.
2. Automation and the Rise of Autonomous Machining
Automation has long been a key factor in the efficiency of precision machining, but recent innovations have taken it to new heights. Autonomous machining systems, powered by AI and advanced robotics, are now capable of operating 24/7 without human intervention. These machines are designed to perform complex tasks such as tool changes, quality control, and even maintenance autonomously, significantly reducing labor costs and production downtime.
Advanced robotic arms with precision sensors and actuators are being integrated into machining systems to handle delicate processes that require extreme accuracy. In some cases, these robotic systems can even make real-time adjustments during the machining process, ensuring optimal outcomes. With digital twins, virtual simulations of machining environments can be created, allowing manufacturers to test and optimize machining processes before they are implemented on the production floor.
3. The Drive Toward Sustainable Precision Machining
Sustainability has become a core focus for manufacturers across industries, and precision machining is no exception. As environmental concerns grow, there is increasing pressure on manufacturers to reduce waste, energy consumption, and carbon emissions. Precision machining technologies are responding with eco-friendly innovations that enhance sustainability without compromising performance.
One of the most promising developments in this area is dry machining, which eliminates the need for coolants and lubricants that can be harmful to the environment. Instead, advanced cutting tools and materials are being developed that can handle high temperatures without the need for these fluids. Additionally, energy-efficient machines that optimize power consumption during operations are gaining popularity, helping manufacturers meet environmental regulations and reduce operational costs.
Another area of focus is material efficiency. As precision machining increasingly incorporates recycled materials and biodegradable composites, industries are finding ways to minimize material waste while maintaining the high levels of quality and precision required for their products.