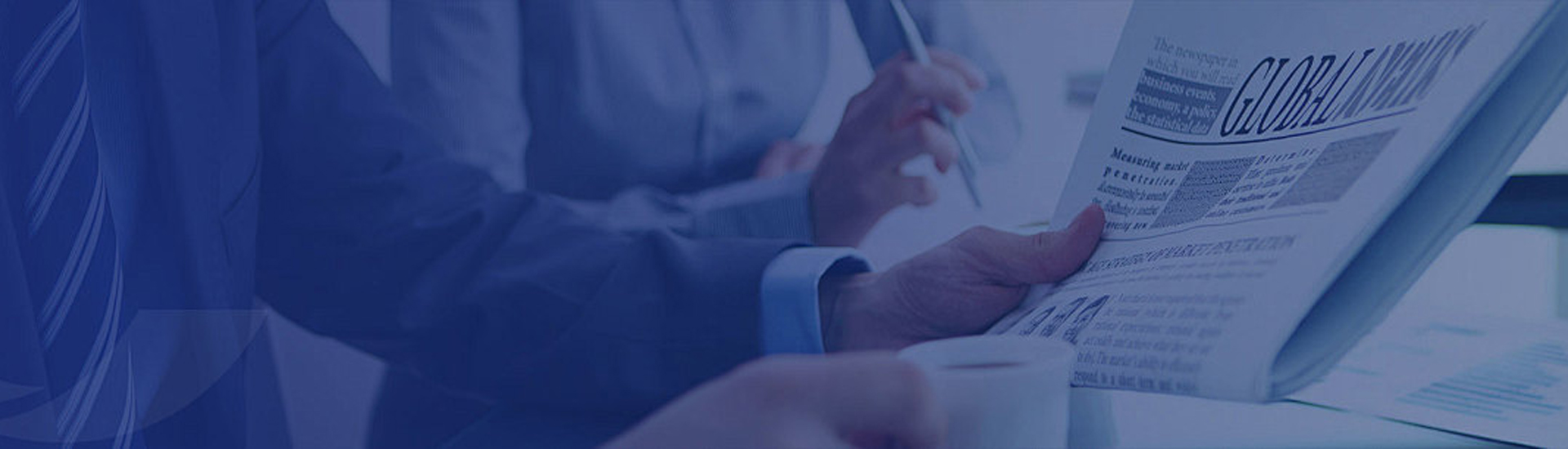
The synergistic development of high-precision machine tools and precision machining2024-10-22
The Evolution of High-Precision Machine Tools in Modern Manufacturing
In the ever-evolving landscape of modern manufacturing, one of the most significant advancements has been the rise of high-precision machine tools. These tools are not only reshaping industries but are also the backbone of a new era in precision machining, where accuracy is paramount and even the tiniest deviation can result in critical consequences. Precision machining refers to the process of producing components with an extremely tight tolerance, and it thrives on the support of high-precision machine tools. Together, their development has formed a synergistic relationship that is continuously pushing the boundaries of what is possible in manufacturing.
The Role of High-Precision Machine Tools in Industry
High-precision machine tools are designed to handle detailed tasks with incredible accuracy, often within micrometers (one-millionth of a meter). These tools are essential in industries like aerospace, automotive, medical devices, and electronics, where intricate designs and complex geometries demand flawless execution. Over the past decades, the demand for high-performance products with minimal margin for error has driven the evolution of machine tools. The integration of advanced technology, such as computer numerical control (CNC), laser guidance, and automated systems, has dramatically enhanced the capabilities of these tools.
Traditionally, machining relied on manual control, with machinists operating lathes, mills, and grinders to produce parts. However, human limitations in accuracy and endurance meant that even the most skilled machinist could not compete with the precision that modern machines now offer. High-precision machine tools not only meet the needs of mass production but also ensure uniformity and perfection in every component, something that is indispensable for the competitive industries of today.
The Emergence of CNC Technology
One of the landmark advancements in this field has been the introduction of CNC technology. CNC machines have become a vital part of the precision machining world because of their ability to automate complex processes. CNC machines follow coded instructions to move tools, allowing them to perform intricate tasks like cutting, drilling, and shaping materials with absolute precision.
Before CNC, manual controls were prone to errors, inconsistencies, and required significant human oversight. CNC machines transformed this process, allowing for a high degree of repeatability, precision, and the ability to create complex geometries that were nearly impossible to achieve using manual tools. The impact of CNC machines has been profound: not only have they dramatically improved the speed of production, but they have also reduced human error, leading to more reliable and durable products. Today, CNC machining is synonymous with high precision.
Moreover, the continual refinement of CNC technology has allowed for even more complex machine configurations, such as 5-axis CNC machining, which provides simultaneous control over multiple axes of movement. This versatility allows machinists to create highly complex parts with minimal setup and eliminates the need for multiple setups in different machines.
Laser-Guided Systems and Digital Integration
Beyond CNC, the integration of laser-guided systems and digital feedback mechanisms has further improved precision machining. Lasers can measure surfaces with extreme accuracy and provide real-time data that can be fed back into the machine's control system. This feedback loop ensures that any minute deviations from the desired outcome can be immediately corrected, allowing for tighter tolerances and finer finishes.
Digitalization has also enabled machine tools to operate autonomously for extended periods, leveraging artificial intelligence (AI) and machine learning (ML) algorithms to predict and mitigate potential issues before they become problems. With the integration of IoT (Internet of Things) technologies, machine tools are now part of smart manufacturing ecosystems where data-driven decisions are made instantaneously to optimize processes, enhance efficiency, and reduce downtime.
Materials Driving the Demand for Precision
The types of materials being used in high-precision machining are another driving force behind the development of advanced machine tools. Traditional metals like steel and aluminum have long been staples in manufacturing. However, the increasing use of advanced materials such as titanium, composites, and ceramics in sectors like aerospace and medical technology has posed new challenges for machining processes.
These materials often have unique properties – such as hardness, brittleness, or heat resistance – that make them more difficult to work with than traditional metals. High-precision machine tools, equipped with cutting-edge technology like high-speed spindles, advanced cooling systems, and vibration dampening, are essential for machining these materials without compromising on quality or performance.
Precision Machining in the Age of Customization
Another notable trend that has influenced the evolution of machine tools is the growing demand for customization. As industries move towards more personalized products – such as custom medical implants, bespoke automotive parts, and tailored aerospace components – the need for flexibility in precision machining has surged.
High-precision machine tools are at the forefront of this shift, offering the versatility needed to produce one-off items or small batches of highly customized products. As the market for individualized, high-precision components grows, manufacturers are increasingly relying on these tools to meet demand without sacrificing efficiency or quality.
The Symbiotic Relationship Between Machine Tools and Precision Machining
As high-precision machine tools evolve, they continually push the boundaries of precision machining, creating a powerful feedback loop of innovation and refinement. Machine tools enable precision machining, and advancements in machining practices, in turn, demand ever-more sophisticated tools. This symbiotic relationship is transforming industries, driving down costs, enhancing product quality, and making previously unimaginable designs a reality.
Enhancing Accuracy and Reducing Waste
The relationship between high-precision machine tools and precision machining is particularly evident in the drastic reduction of waste. In traditional machining, even small errors can lead to material wastage, driving up costs, and increasing production times. High-precision machine tools minimize this waste by ensuring that each cut, drill, or shaping operation is performed exactly as required, reducing the need for rework or discarding defective parts.
This reduction in waste is especially significant in industries such as aerospace and medical devices, where the materials used are often expensive, and errors can be catastrophic. For example, producing a titanium component with a minor error could result in thousands of dollars in material loss and hours of production time wasted. With high-precision machining, these risks are greatly minimized, leading to lower costs and higher profit margins for manufacturers.
Additionally, the rise of additive manufacturing (3D printing) as a complement to traditional subtractive precision machining has enabled manufacturers to further reduce waste. High-precision machines are often used to finish parts created through 3D printing, combining the strengths of both technologies to create parts that are highly efficient to produce and require minimal material.
Automation and Smart Manufacturing
Automation has become a cornerstone of the modern manufacturing environment, and high-precision machine tools have played a pivotal role in this transformation. The ability to automate precision machining processes not only reduces labor costs but also enhances consistency and quality. By removing the variability introduced by human intervention, manufacturers can ensure that every component meets exact specifications, regardless of the production volume.
Smart manufacturing, often referred to as Industry 4.0, is taking this a step further by integrating machine tools into larger, interconnected systems. In a smart factory, machine tools are part of a network where data flows freely between different machines and production stages. This allows for real-time monitoring, predictive maintenance, and optimization of production processes.
Machine tools equipped with sensors and connected to IoT platforms can analyze their own performance and detect potential issues before they lead to machine failure or product defects. This self-monitoring capability leads to greater uptime and significantly reduces the risk of production delays. Furthermore, machine learning algorithms can analyze the vast amounts of data generated by these machines to further optimize processes, identifying the most efficient ways to produce high-precision parts.
Challenges and Opportunities Ahead
Despite the incredible advancements in high-precision machine tools and precision machining, challenges still remain. For one, the initial cost of acquiring and maintaining these advanced machines can be prohibitive, especially for smaller manufacturers. However, as the technology continues to mature and become more widely adopted, costs are expected to decrease, making high-precision tools more accessible to a broader range of industries.
Another challenge is the need for skilled labor to operate, maintain, and program these sophisticated machines. While automation is reducing the need for manual intervention, there is still a demand for highly trained technicians who can troubleshoot problems, optimize performance, and ensure that machines are functioning at peak efficiency.
Looking to the future, there are tremendous opportunities for further integration of AI, machine learning, and robotics into precision machining. As these technologies advance, we can expect to see even greater automation, improved machine learning models that can predict and prevent defects, and smarter machine tools capable of operating with minimal human input.
In conclusion, the synergistic development of high-precision machine tools and precision machining has created a feedback loop of continuous improvement, driving industrial innovation. This dynamic relationship is transforming industries, enhancing product quality, reducing waste, and making once-impossible designs a reality. As this trend continues, we can only expect the role of high-precision tools in manufacturing to become even more critical, pushing the boundaries of what's possible in the world of engineering and production.