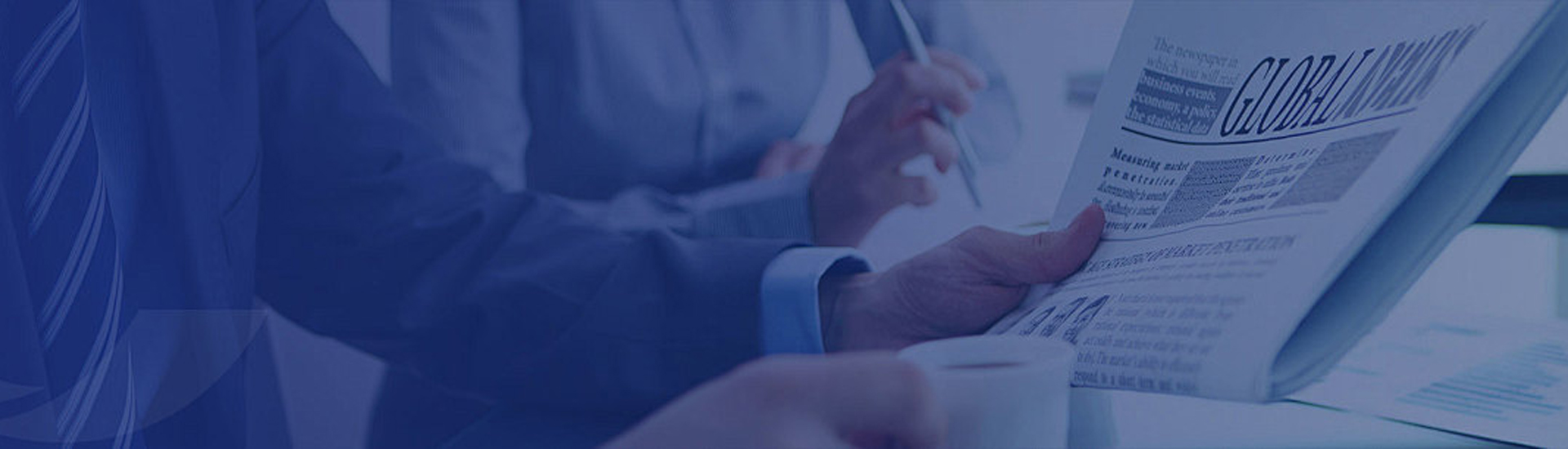
The key role of precision machining in the manufacture of new energy vehicle batteries2024-10-21
The shift towards new energy vehicles (NEVs) has sparked tremendous innovation across the automotive industry. One of the most critical yet often overlooked factors driving this revolution is precision machining. This article explores how precision machining technology plays an indispensable role in the production of NEV batteries, enhancing their efficiency, reliability, and performance.
Precision machining, new energy vehicle batteries, NEV production, battery manufacturing, automotive innovation, green technology, sustainable energy, battery technology, electric vehicles
Precision Machining – The Backbone of New Energy Vehicle Battery Manufacturing
In the rapidly evolving world of electric vehicles (EVs) and new energy vehicles (NEVs), the focus on sustainability and efficiency has never been greater. At the heart of this transformative shift lies one of the most vital components—the battery. Battery technology is the lifeblood of NEVs, dictating their range, performance, safety, and cost-effectiveness. While much attention is given to battery chemistry, design, and materials, the role of precision machining in battery manufacturing is equally crucial, albeit often underappreciated.
Precision machining, a manufacturing process that utilizes advanced tools and techniques to shape and finish components to incredibly tight tolerances, plays an indispensable role in the production of high-quality batteries for NEVs. It ensures that each component is manufactured with exceptional accuracy, contributing to the overall efficiency, durability, and safety of the final product. This article delves into how precision machining is transforming NEV battery production, enabling the industry to meet the demands of today’s eco-conscious consumers while pushing the boundaries of technological innovation.
The Need for Precision in Battery Manufacturing
Manufacturing batteries for NEVs is a complex process that requires absolute precision at every stage. Unlike conventional vehicles powered by internal combustion engines, electric vehicles rely entirely on their batteries for propulsion, making battery performance a critical factor in determining the success of an NEV. To optimize performance, manufacturers must produce batteries that are lightweight, energy-dense, and reliable, all while keeping costs in check.
Precision machining meets these requirements by enabling the production of battery components with minimal deviation from design specifications. From the cathode and anode plates to the battery casing and cooling systems, every element of an NEV battery must fit together perfectly to ensure optimal functionality. Even a slight misalignment or imperfection in the battery’s structure can result in decreased performance or, worse, safety hazards such as overheating or short-circuiting.
The tolerances required in battery manufacturing are incredibly tight—often within microns—making precision machining an essential process. Whether it’s cutting, drilling, or milling, precision machining ensures that components meet exact specifications, which is crucial for creating the high-quality, consistent products needed to power the next generation of vehicles.
Enhancing Energy Density and Performance
One of the primary goals in NEV battery development is to increase energy density—the amount of energy that can be stored in a given volume or weight of battery. Higher energy density translates into longer driving ranges for electric vehicles, which is a key concern for consumers. However, achieving higher energy density requires more than just advances in battery chemistry; it also demands meticulous manufacturing processes that can support the creation of compact, high-capacity cells.
Precision machining plays a pivotal role in this aspect by enabling the production of ultra-thin and lightweight battery components without compromising strength or durability. For instance, precision machining tools can create thinner electrode plates, allowing for more layers of active materials to be packed into each battery cell, thereby increasing its capacity. Furthermore, precision machining is essential for producing intricate cooling systems, which help manage heat buildup in high-energy-density batteries, ensuring that they operate safely and efficiently.
In addition to increasing energy density, precision machining also contributes to the overall performance of NEV batteries. By ensuring that every component fits together seamlessly, precision machining reduces internal resistance within the battery, which improves energy transfer and extends the vehicle’s range. It also enhances the durability of the battery, allowing it to withstand the rigors of daily use without significant degradation in performance.
Battery Safety and Reliability – A Key Focus
Safety is a paramount concern in the development of NEV batteries, particularly given the potential risks associated with thermal runaway—a situation where a battery overheats and can potentially catch fire or explode. To mitigate these risks, manufacturers rely heavily on precision machining to produce battery components with exacting standards that minimize the chances of failure.
For instance, precision machining is used to manufacture the housing that encases each battery cell, ensuring that it is robust enough to contain any potential hazards while still being lightweight and compact. The precision with which these casings are manufactured is critical, as even the smallest defect could compromise the integrity of the battery and lead to dangerous malfunctions.
Additionally, precision machining enables the production of highly effective thermal management systems, which are essential for maintaining the safe operation of NEV batteries. These systems, often composed of intricate channels and cooling plates, help dissipate heat generated during the charging and discharging cycles, preventing overheating and ensuring that the battery operates within a safe temperature range.
As the demand for electric vehicles continues to grow, the importance of precision machining in ensuring the safety and reliability of NEV batteries cannot be overstated. By producing components that meet the highest standards of accuracy and quality, precision machining helps manufacturers deliver batteries that consumers can trust.
Innovation in Precision Machining for NEV Batteries
As the new energy vehicle market expands, so too does the need for innovation in manufacturing processes. Precision machining is no longer confined to traditional cutting, milling, and drilling techniques; it is now at the forefront of cutting-edge manufacturing technologies that are shaping the future of NEV battery production. In this section, we explore some of the latest advancements in precision machining and their impact on NEV battery manufacturing.
Laser Machining – A Game Changer for Battery Production
One of the most significant advancements in precision machining for NEV batteries is the use of laser machining technology. Lasers offer unparalleled precision, allowing manufacturers to create complex geometries and ultra-fine features that would be impossible to achieve with conventional methods. This makes laser machining ideal for producing critical components of NEV batteries, such as electrode foils and separator membranes.
Laser machining provides several key benefits in battery manufacturing. First, it enables the creation of ultra-thin materials with high dimensional accuracy, which is essential for producing high-energy-density batteries. Second, laser machining is a contactless process, meaning there is minimal risk of damaging delicate materials during fabrication. This is particularly important when working with the thin, fragile layers of active materials used in modern battery cells.
Moreover, laser machining can be used to precisely cut cooling channels and other intricate features in the battery casing, helping to improve thermal management and enhance the overall efficiency of the battery. As manufacturers strive to meet the growing demand for high-performance NEV batteries, laser machining is proving to be a game changer, enabling the production of components with unprecedented precision and quality.
Additive Manufacturing – Pushing the Boundaries of Design
Another exciting development in precision machining for NEV batteries is the rise of additive manufacturing, commonly known as 3D printing. Additive manufacturing allows for the creation of highly complex, custom-designed components that would be difficult or impossible to produce using traditional machining methods. This opens up new possibilities for optimizing battery design and improving performance.
For example, additive manufacturing can be used to produce lightweight, high-strength battery casings that reduce the overall weight of the vehicle without compromising safety or durability. It can also be used to create custom cooling systems with optimized geometries, improving heat dissipation and enhancing the battery’s operational efficiency.
Additionally, additive manufacturing allows for rapid prototyping, enabling manufacturers to test and iterate new battery designs quickly. This is particularly valuable in the fast-paced NEV market, where innovation is key to staying competitive. By leveraging additive manufacturing, battery manufacturers can bring new products to market faster while ensuring that they meet the highest standards of quality and performance.
Automation and AI-Driven Machining
Automation and artificial intelligence (AI) are transforming the precision machining industry, bringing a new level of efficiency and consistency to the manufacturing of NEV batteries. AI-driven machining systems can analyze vast amounts of data in real-time, making adjustments to the machining process to ensure that each component is produced with the highest possible precision.
Automated precision machining systems can also operate 24/7, significantly increasing production capacity and reducing lead times. This is critical in the NEV market, where demand for high-quality batteries is skyrocketing. By incorporating automation into the machining process, manufacturers can scale up production without sacrificing quality, helping to meet the growing demand for electric vehicles.
Furthermore, AI-driven machining systems can predict potential defects or deviations in the production process before they occur, reducing the risk of costly errors and ensuring that each battery component meets the necessary specifications. This level of precision and consistency is essential for producing reliable, high-performance NEV batteries that consumers can depend on.
Conclusion: Precision Machining – The Future of NEV Battery Production
The future of new energy vehicles depends on the development of advanced battery technologies, and precision machining is playing a key role in making this future a reality. From enhancing energy density and performance to improving safety and reliability, precision machining is at the heart of NEV battery production. With continued advancements in laser machining, additive manufacturing, and AI-driven processes, precision machining will remain an essential driver of innovation in the NEV industry for years to come.
As the world moves towards a greener, more sustainable future, the importance of precision machining in the manufacture of new energy vehicle batteries cannot be overstated. By enabling the production of high-quality, high-performance batteries, precision machining is helping to power the vehicles of tomorrow and pave the way for a more sustainable future.
By integrating both parts, this article covers the entire spectrum of how precision machining contributes to NEV battery production, from improving energy density and safety to driving technological innovation.