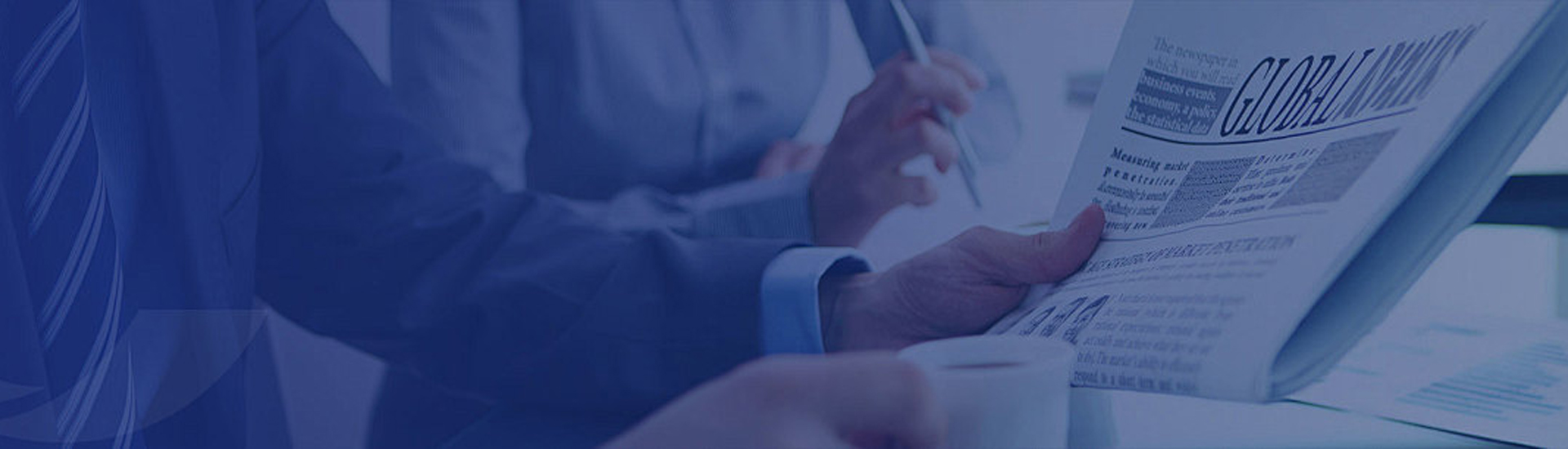
The key role of precision machining in mould manufacturing2024-10-21
Precision Machining – Transforming Mould Manufacturing
In today's fast-paced manufacturing industry, precision machining has become the backbone of mould manufacturing, offering unmatched accuracy, efficiency, and consistency. Moulds are fundamental to producing everything from simple plastic items to complex automotive components. The evolution of modern mould manufacturing has been driven by the need for greater precision, reduced lead times, and more reliable production processes. Precision machining, with its advanced technologies and processes, plays a pivotal role in meeting these demands.
What Is Precision Machining?
Precision machining refers to the process of shaping materials into exact dimensions and tolerances, often involving highly sophisticated machinery and computer-controlled systems such as CNC (Computer Numerical Control) machines. The essence of precision machining lies in its ability to produce intricate parts and components with extreme accuracy. In mould manufacturing, where complex geometries and fine details are required, precision machining is indispensable.
By using precision machining techniques, mould makers can create parts with minimal deviations, ensuring perfect fits and reducing the need for secondary operations. The enhanced control over dimensions and surface finishes means that products derived from moulds exhibit higher quality and reliability.
The Role of Precision Machining in Mould Manufacturing
One of the most critical applications of precision machining in mould manufacturing is the creation of complex, high-performance moulds for industries such as automotive, aerospace, medical devices, and consumer goods. Here's why it matters:
Tighter Tolerances: In mould manufacturing, tight tolerances are essential. Precision machining ensures that the mould components meet the required specifications down to micrometers. This is crucial in sectors where even the slightest deviation can lead to product failure, such as aerospace and medical devices.
High Complexity and Intricacy: As product designs become more complex, the moulds used to create them must also be able to accommodate intricate details. Precision machining allows manufacturers to produce complex mould shapes with ease, enabling the creation of more sophisticated products.
Improved Surface Quality: The surface quality of a mould is vital because it directly affects the finish of the end product. Precision machining can achieve exceptional surface finishes, often eliminating the need for additional polishing or post-processing steps.
Cost Efficiency: Precision machining minimizes waste by maximizing material usage and reducing the likelihood of errors during production. Although the initial investment in advanced CNC machines and precision machining equipment can be high, the long-term cost savings in terms of material efficiency, reduced rework, and faster production cycles justify the investment.
Key Technologies Driving Precision Machining in Mould Manufacturing
Several cutting-edge technologies have been at the forefront of precision machining in mould manufacturing. Among them are:
CNC Machining: CNC machines have revolutionized the way moulds are produced. These computer-controlled machines allow for highly automated and repeatable processes, significantly increasing the precision and consistency of the final product. With CNC machining, manufacturers can easily switch between different mould designs and specifications, making it ideal for custom or low-volume production.
Electrical Discharge Machining (EDM): EDM is a non-contact machining process that is particularly useful for working with hard or heat-resistant materials. In mould manufacturing, it allows for the production of intricate mould cavities and features that are difficult to achieve with traditional machining methods.
Laser Machining: Laser technology is another important tool in precision machining. It can be used to cut, engrave, or mark mould surfaces with high accuracy, often at micron-level precision. This is especially valuable for creating detailed mould designs and ensuring uniformity across large production runs.
3D Printing and Additive Manufacturing: Although primarily used for prototyping, additive manufacturing is increasingly being integrated into mould production. It can create highly complex mould components with greater flexibility, and when combined with precision machining, it offers even higher accuracy and reduced material wastage.
These technologies enable mould manufacturers to push the boundaries of what is possible, delivering high-performance, long-lasting moulds that meet the rigorous demands of today’s industries.
The Advantages of Precision Machining in Mould Manufacturing
As manufacturing trends continue to evolve, precision machining remains at the forefront of innovation. Its application in mould manufacturing not only ensures the creation of high-quality moulds but also brings several tangible benefits that enhance the overall efficiency and competitiveness of manufacturers.
1. Increased Production Speed
One of the most significant advantages of using precision machining in mould manufacturing is the ability to drastically reduce lead times. CNC machines, in particular, can operate continuously with minimal supervision, allowing for the rapid production of moulds. Furthermore, the precision of these machines means that fewer adjustments are needed during the manufacturing process, speeding up production cycles. This improved efficiency enables manufacturers to respond quickly to market demands and reduces downtime, giving companies a competitive edge.
2. Enhanced Flexibility and Customization
Modern industries demand greater flexibility in production, as customization becomes increasingly important. Precision machining makes it possible to create moulds that are tailored to specific requirements with minimal setup changes. Whether a company needs a single custom mould or large-scale production of complex designs, precision machining allows for quick adaptation to different designs without compromising on quality. This flexibility is vital in industries such as consumer electronics, where product designs change rapidly, and time-to-market is critical.
3. Higher Durability and Longevity
Moulds produced using precision machining tend to have longer lifespans due to the high-quality materials and exacting standards used in their creation. This is especially important in industries that require mass production, such as automotive or packaging, where moulds are subject to continuous use. Precision-machined moulds can withstand more wear and tear, reducing the need for frequent replacements and downtime, ultimately lowering operational costs.
4. Sustainability and Material Efficiency
As companies strive to reduce their environmental impact, precision machining offers a solution by minimizing material waste. The ability to work with tight tolerances ensures that only the necessary amount of material is used, reducing scrap and conserving valuable resources. Additionally, precision machining often involves less energy consumption than traditional manufacturing methods due to its increased efficiency, further supporting sustainable manufacturing practices.
5. Reduced Risk of Errors and Defects
The high level of accuracy and consistency provided by precision machining significantly lowers the risk of errors and defects in mould production. Traditional manufacturing methods can sometimes lead to variations that affect the final product quality. However, precision machining's automated systems and detailed programming virtually eliminate these risks, ensuring that each mould produced is identical and free from imperfections. This is crucial in industries such as medical devices, where the safety and efficacy of products depend on flawless manufacturing.
Looking Ahead: The Future of Precision Machining in Mould Manufacturing
The future of precision machining in mould manufacturing is set to be even more exciting as emerging technologies such as artificial intelligence (AI), machine learning, and advanced automation come into play. These innovations will allow manufacturers to push precision and efficiency to new heights, further reducing production times and improving overall quality.
Additionally, as the demand for lightweight, complex, and miniaturized products grows, precision machining will continue to play a key role in enabling manufacturers to meet these challenges. By embracing cutting-edge techniques and technologies, the mould manufacturing industry is poised for continued growth and success.
In conclusion, precision machining is indispensable in modern mould manufacturing. Its ability to deliver high accuracy, reduce waste, and increase production efficiency makes it a cornerstone of industrial production. As technology continues to evolve, precision machining will remain at the forefront, driving innovation and shaping the future of manufacturing across multiple industries.