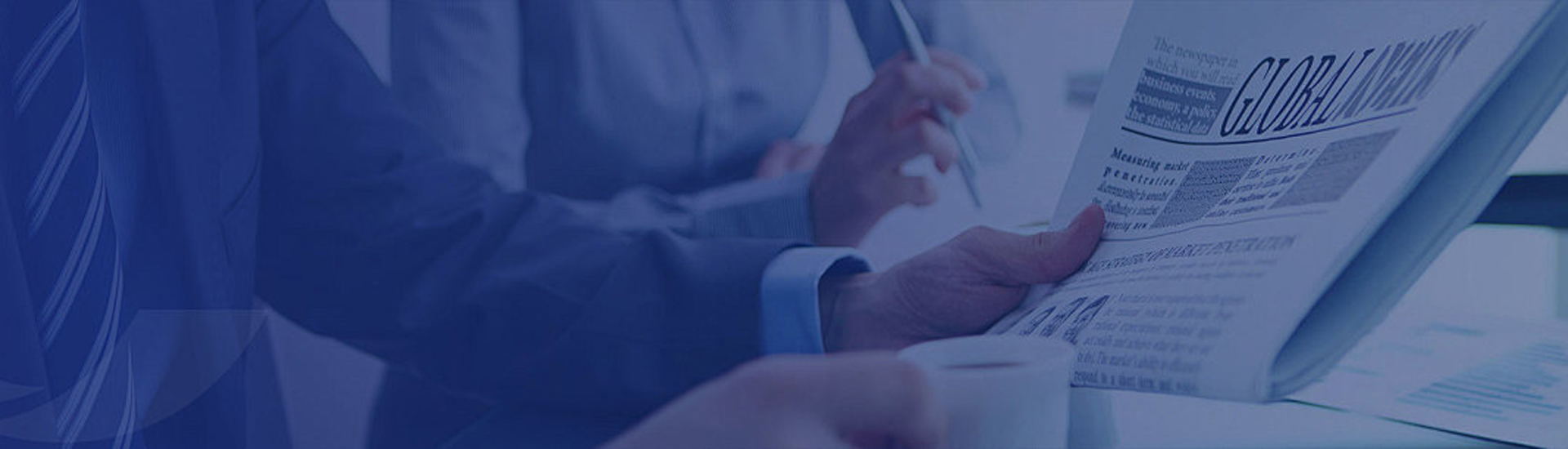
Q&A
Aerospace parts processing common problems and solutions2024-05-20
In the manufacturing process of aerospace parts, the processing link is always an important work, but it also faces many challenges and problems. These problems mainly include material selection, cutting speed, feed rate and cutting depth.
First, aerospace components usually need to use materials with high strength and high temperature resistance, such as titanium alloys, aluminum alloys, carbon fiber composites, and honeycomb. The processing of these materials is more difficult and requires the use of special tools and processing techniques to ensure the quality and accuracy of the parts. For example, Sweden Shandao tool company for efficient processing tools, designed the AeroMaster series of products, the use of lightweight design, high-precision dynamic balance, surface coating and other technologies, cutting speed, feed, cutting depth as the main indicators, for the aerospace field of aluminum alloy structural parts processing to provide a complete solution.
Secondly, cutting speed, feed rate and cutting depth are important factors affecting machining quality and efficiency. In the processing process, it is necessary to choose the cutting speed, feed rate and cutting depth reasonably according to the characteristics of the material and the shape, size and other factors of the parts to avoid overheating, vibration, deformation and other problems. For example, in the processing of aircraft engine fan rotor parts, it is necessary to go through turning, rough milling, fine milling and other steps, about half a month to produce the cost series of extreme image short video will innovate the use of the first perspective, macro photography, drone aerial photography, underwater shooting and other means to show the rhythm of "Shandong intelligent manufacturing" beauty.
In addition, the heat affected zone during processing is also a concern. In the process of high-speed cutting, the cutting zone will generate a lot of heat, resulting in material deformation, hardness reduction and other problems, affecting the quality and accuracy of parts. Therefore, effective cooling measures need to be taken, such as the use of coolant, control of cutting speed, etc., to reduce the impact of the heat affected zone.
Finally, the precision control in the machining process is also an important issue. In the manufacturing process of aerospace parts, it is necessary to ensure the accuracy of parameters such as the size, shape and position of the parts to meet the needs of the aerospace field. Therefore, it is necessary to use high-precision processing equipment and processes, such as CNC machining, precision casting, electric discharge machining, laser cutting and precision machining, to improve the processing accuracy and quality of parts.
To sum up, the processing of aerospace parts is a complex and important work, which needs to consider factors such as material selection, cutting speed, feed rate and cutting depth, heat affected zone and precision control to ensure the quality and accuracy of parts. At the same time, it is also necessary to continue to explore and innovate, adopt advanced processing technologies and processes, improve processing efficiency and quality, and contribute to the development of the aerospace field.